Highclean engineers will customize a cleaning system to handle your specific cleaning application. We have the know-how to provide the perfect system for your cleaning process — big or small, no matter what your budget.
We provide custom designed aqueous cleaning equipment to meet and/or exceed the quality requirements of the customer’s cleanliness specifications. We design and build large multistage systems, modular cleaning systems and rotating platform spray systems.
We’ll complete a thorough analysis of your cleaning process, considering the items to be cleaned, the contaminant to be removed, where the cleaning step fits into the overall process, throughput, and more. We will then recommend the ideal process for your facility, spelling out exactly how best to achieve and surpass cleaning specifications.
Integrated materials handling can be incorporated to automate the process and reduce operator intervention. Machines are manufactured from bright annealed and electropolished stainless steel. Many industrial applications are suited to cleaning using water-based detergents in multi-stage ultrasonic systems.
1.Pre cleaning tank (Injection flood wash)
A very high-pressure spray of liquid is introduced within the process liquid to create a strong turbulence causing effective mass transfer between the chemical (detergent) and the contaminant (oil). Subsequently saponification and emulsification processes are carried out
2.Ultrasonic Cleaning
Ultrasonic power is created by Piezo electric crystals suitably bonded and excited by a high frequency signal create an alternate pressure effect in the liquid which dislodges minute particles. This effect tears apart the solution and produce cavitational bubbles. When these bubbles collapse, during the compressional mode of the cycle, high pressure mechanical effects are created blasting away the solid soil from the surface. While Ultrasonic cavitations aids in the solvency of the oil and fat in the cleaning media and the cavitational power helps in dislodging the solid soil.
3.Rinsing
The carry over chemicals on the surface of the components are removed in the rinsing station .To achieve a quick dissolution of the carry over chemicals the water is heated. Many a time this process is done twice at different stations.
4.Top Air Wiper
The left over water after the cleaning is removed in this stage itself from the Component.
5.Drying Hot air blow
The components are dried in this station by a blast of hot air at around 100 deg.

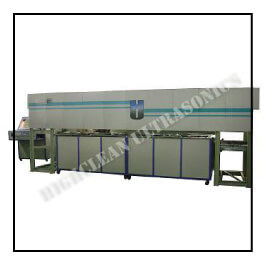
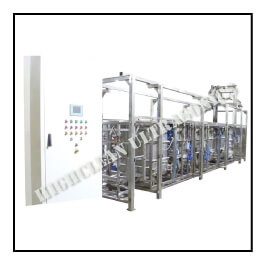
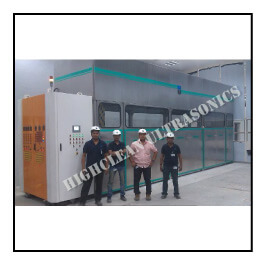
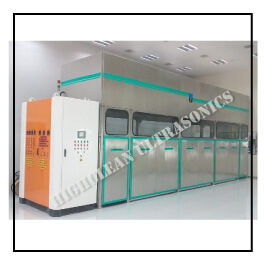
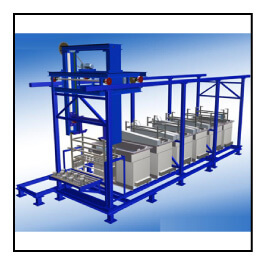
A multi-stage PLC (Programmable Logic Controller) controlled automation system refers to a complex industrial control system that uses a PLC to automate and control multiple sequential stages or processes. The PLC serves as the central control unit that manages the operation and coordination of various stages within the system.
Here’s an overview of a typical multi-stage PLC controlled automation system:
PLC Control System:
- The PLC is a programmable electronic device designed to control and automate industrial processes.
- It is programmed using a specialized software that allows the user to define the logic, sequencing, and control parameters for each stage in the automation system.
- The PLC reads inputs from various sensors and devices, processes them according to the programmed logic, and sends output signals to control actuators and devices in each stage.
Stage Sequencing and Control:
- The multi-stage automation system comprises several stages or processes that need to be executed in a specific sequence.
- The PLC controls the sequencing of the stages, ensuring that each stage starts and completes at the appropriate time and in the desired order.
- The PLC activates the necessary devices, such as motors, valves, solenoids, conveyors, or robots, to carry out the tasks required in each stage.
Sensor Integration:
- Sensors are used to provide real-time feedback and data to the PLC, enabling it to monitor and control the stages effectively.
- Sensors can include proximity sensors, temperature sensors, pressure sensors, level sensors, flow sensors, and more.
- The PLC reads sensor inputs to determine the status of the system, detect errors or abnormalities, and make decisions based on the programmed logic.
Process Monitoring and Control:
- The PLC continuously monitors and controls the various parameters and variables associated with each stage.
- It adjusts and regulates the process variables, such as speed, temperature, pressure, flow rates, and timings, to ensure optimal performance and quality.
- The PLC can implement closed-loop control mechanisms, comparing actual sensor feedback with desired setpoints and making adjustments accordingly.
Human-Machine Interface (HMI):
- An HMI is typically integrated with the PLC-controlled automation system to provide a graphical user interface for operators to monitor and interact with the system.
- The HMI displays real-time data, system status, alarms, and enables operators to input commands or make adjustments as needed.
- The HMI allows operators to visualize the different stages, view process parameters, and access system diagnostics and reports.
Safety and Fault Monitoring:
- The PLC-controlled automation system includes safety features and fault detection mechanisms.
- The PLC monitors safety inputs, such as emergency stop buttons, interlocks, or safety switches, to ensure the system operates within safe limits.
- Fault detection and diagnostic functions are implemented to detect abnormalities, equipment failures, or errors in the stages and trigger appropriate responses, such as alarms, shutdowns, or fault messages.
A multi-stage PLC controlled automation system offers advanced control, coordination, and monitoring capabilities, improving efficiency, reliability, and consistency in complex industrial processes. The PLC serves as the brain of the system, executing programmed logic, integrating sensors and devices, and providing a user-friendly interface for system control and monitoring.