Under precious guidance of our skilled professionals, we are engaged in offering a wide range of Wire Dies CleaningSystem that is widely for flawless cleaning in wire industries. Owing to their remarkable quality, the offered product is widely demanded in the market. This product is manufactured by our experienced professionals using premium quality raw materials and progressive technology. Moreover, we check that this product on various parameters to make a flawless dispatch from our end.
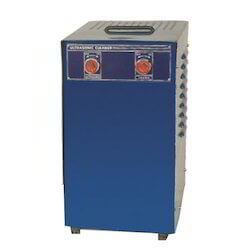
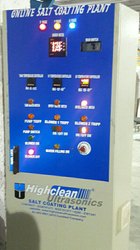
Our team of HIGHCLEAN ULTRASONICS by utilizing years of experience, we bring forth a qualitative array of online steel wire coating plant .The offered coating is manufactured utilizing superior quality raw materials and latest technology. Moreover, a team of our quality controllers conducts a series of quality tests on the entire range to seek out any possible defect. In tune with international standard, we provide this product in various customized options and industrial leading prices.
A wire die cleaning system is a specialized machine used to clean and maintain wire drawing dies. Wire drawing dies are precision tools used in the wire manufacturing industry to reduce the diameter of wire by pulling it through a series of dies. Over time, wire drawing dies can accumulate contaminants, such as metal shavings, lubricants, and debris, which can affect the wire quality and the performance of the dies. A wire die cleaning system provides an efficient and automated solution for cleaning and maintaining these critical components. Here are some key features and considerations of a wire die cleaning system:
Cleaning Process: The wire die cleaning system typically utilizes a combination of cleaning methods, including ultrasonic cleaning, brushing, flushing, and drying. The dies are placed in a cleaning chamber or fixture, where they undergo a series of cleaning stages to remove contaminants and restore their optimal performance.
Ultrasonic Cleaning: Ultrasonic cleaning is a common method used in wire die cleaning systems. The system generates high-frequency sound waves that create cavitation in a cleaning solution, dislodging contaminants from the surface of the dies.
Brushing: The wire die cleaning system may incorporate brushing mechanisms to mechanically scrub the dies. This can help remove stubborn or adhered contaminants, such as metal shavings or residual lubricants.
Flushing: The cleaning system may include a flushing mechanism that uses jets of cleaning solution or water to rinse away loosened contaminants from the wire dies.
Drying: After the cleaning process, the wire dies need to be thoroughly dried to prevent corrosion and ensure optimal performance. The cleaning system may include a drying mechanism, such as hot air or forced air drying, to remove excess moisture from the dies.
Cleaning Solution: The cleaning solution used in the wire die cleaning system is crucial for effective cleaning. It is typically formulated with chemicals that can dissolve or emulsify the contaminants without causing damage to the wire dies. The specific cleaning solution will depend on the type of contaminants and the material of the wire dies.
Automation and Control: Wire die cleaning systems often incorporate automation features and control systems to streamline the cleaning process. These may include programmable settings, timers, and monitoring capabilities to ensure consistent and efficient cleaning results.
Safety Features: The wire die cleaning system may include safety features to protect operators and prevent accidents. This can include safety interlocks, emergency stop buttons, or protective enclosures to minimize exposure to hazardous chemicals or moving parts.
When selecting a wire die cleaning system, it is important to consider factors such as the size and type of wire dies to be cleaned, the desired cleaning efficiency, production volume, and any specific requirements or regulations related to the cleaning process or the type of contaminants being removed. Consulting with manufacturers or suppliers of wire drawing equipment can help identify the most suitable wire die cleaning system for a particular application.