Riding on unfathomable volumes of industrial expertise, we are offering an excellent range of PCB Electrical Cleaner. Being a quality-oriented organization, we assure our clients that this product is the best in quality. Thorough ultrasonic cleaning of electronics plays a crucial role in assuring reliability of the finished product. Our skilled professionals only utilize fine quality raw materials, while manufacturing the entire range. Moreover, our offered product can be availed in a wide range of sizes and designs, as per the requirements of our esteemed clients.
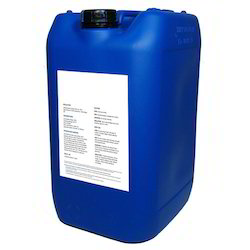
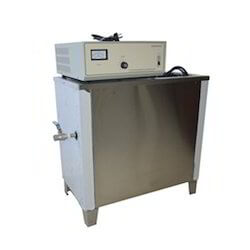
Our reputation in the market is largely attributable to our precision-designed Ultrasonic PCB Wire Cleaner from our extensive collection of products. Our skilled professionals make use of finest grade quality raw materials, coupled with advanced technology to design this cleaner. Cleaning is used for stainless steel, low and high carbon steel, aluminium alloy, copper wire to remove calcium and sodium steerage lubricant residues after the dry drawing process, or lubricant oil from a wet drawing machine or forming process etc. Apart from this, remarkable quality and sturdy structure increase the demand of our offered product in the market.
With enormous experience in this domain, we have established ourselves as the dependable manufacturer, exporter and supplier of precisely designed Ultrasonic PCB Cleaner. Our offered cleaner is manufactured from using superior quality raw materials and advanced technology. While manufacturing the offered cleaner, we lay special emphasis on the overall quality and durability. Ultrasonic PCB Cleaner is normally used for cleaning assembled PCB. Additionally, our quality analysts keep an eye on this cleaner to avoid any possibility of flaw.
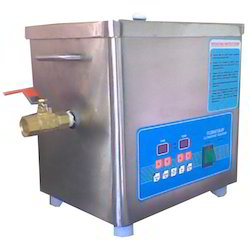
PCB (Printed Circuit Board) cleaners are specifically designed to clean and remove contaminants from PCBs used in electronic devices and equipment. PCBs can accumulate flux residues, soldering residues, dust, oils, and other contaminants during the manufacturing process. Effective cleaning of PCBs is crucial to ensure proper functionality and reliability of electronic circuits. Here are some common types of PCB cleaners:
Solvent-Based PCB Cleaners: Solvent-based cleaners are commonly used to remove flux residues, oils, and other organic contaminants from PCBs. These cleaners typically contain volatile organic compounds (VOCs) and are effective at dissolving and removing contaminants. Popular solvents used in PCB cleaners include isopropyl alcohol (IPA), trichloroethylene (TCE), and naphtha. It is important to use these cleaners in well-ventilated areas and follow safety guidelines when working with VOCs.
Aqueous PCB Cleaners: Aqueous-based cleaners are water-based solutions that are effective in removing both organic and inorganic contaminants from PCBs. These cleaners are environmentally friendly and typically do not contain harsh chemicals. Aqueous cleaners can be used in ultrasonic cleaning systems or through manual application. They often require rinsing with clean water after the cleaning process to ensure the removal of residues.
Semi-aqueous PCB Cleaners: Semi-aqueous cleaners combine the advantages of both solvent-based and aqueous-based cleaners. They are formulated with a blend of solvents and water, offering effective cleaning properties while reducing the use of VOCs. Semi-aqueous cleaners are commonly used for removing flux residues and other contaminants from PCBs.
Cleaning Agents for Specific Contaminants: Some PCB cleaners are specifically formulated to target certain types of contaminants. For example, flux removers are designed to remove flux residues left behind after soldering processes. These cleaners can be solvent-based or aqueous-based, depending on the specific type of flux and the cleaning requirements.
When using PCB cleaners, it is important to follow manufacturer guidelines and recommendations. Here are a few general considerations:
Ensure compatibility: Check that the cleaner is compatible with the materials used in the PCBs, including the solder mask, components, and PCB substrate.
Test on a small area: Before cleaning the entire PCB, it is advisable to test the cleaner on a small, inconspicuous area to ensure it does not cause any damage or adverse effects.
Proper application: Apply the cleaner using appropriate methods, such as brushing, spraying, or immersion, depending on the cleaner and the level of contamination.
Rinse and dry: After cleaning, rinse the PCB thoroughly with clean water or a recommended rinse solution to remove any residual cleaner. Ensure proper drying before reassembly or further processing.
Safety precautions: Follow safety guidelines provided by the cleaner manufacturer, including the use of protective equipment, working in well-ventilated areas, and proper disposal of cleaning waste.
It is essential to choose a PCB cleaner that meets the specific cleaning requirements and quality standards of your PCBs. Manufacturers and suppliers of PCB cleaning products can provide guidance on selecting the most suitable cleaner for your application.