
Ultrasonic cleaning of PCBs is gentle and thorough.
Thorough ultrasonic cleaning of electronics plays a crucial role in assuring reliability of the finished product.Flux removal from assembled and reworked PCBs as well as solder paste removal from misprinted PCBs are critical process steps. An ultrasonic circuit board cleaner removes flux, even tenacious residues from lead-free and low-residue fluxes, from printed circuit boards with either through-hole technology or surface-mount components. Ultrasonic cleaning of electrical components offers clear advantages over spray washing when the components have tight clearances or tubular geometries
- Rapidly achieves high level of cleanliness
- Will not damage delicate assemblies
- Cleans components with blind holes or complex geometries
- Uses aqueous or semi-aqueous cleaners
- Increases reliability of finished electronic products
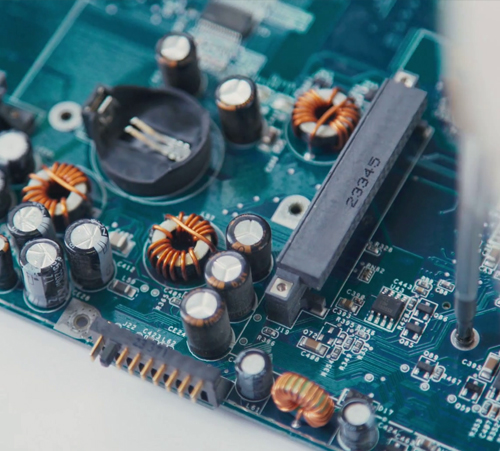
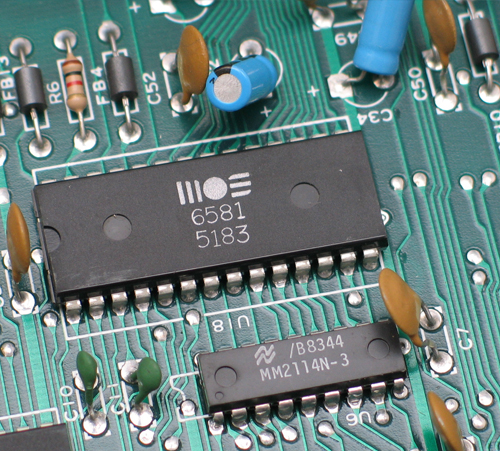
An ultrasonic circuit board cleaner helps to improve SIR test results while reducing rework and increasing PCB reliability. Ultrasonic cleaning electrical assemblies with delicate components is a safe way to remove contaminants from parts easily susceptible to damage. Tiny precision assemblies have inaccessible surfaces that cannot be cleaned by other methods. Electronic devices can be safely cleaned in water with the appropriate chemical agent as long as they are properly dried. Many people hold the belief that electronics cannot be placed in water. This is simply not true. An ultrasonic electronics cleaner can be used quite effectively to maintain and restore a broad range of equipment. We offer products specifically designed for optimum cleaning of circuit boards and electronics. Before the advent of Sweep technology, single-frequency ultrasonic cleaners generated a harmonic wave with the potential to damage electronic components. Our ultrasonic cleaners with Sweep technology eliminate the possibility of this type of damage.
Cleaning Electronics with an Ultrasonic Cleaner
Ultrasonic cleaning has become one of the most popular ways to clean electronics. The process saves time and improves results without compromising safety. Let’s take a quick look at how an ultrasonic electronics cleaner can be used effectively for circuit boards, PCB, and electrical assemblies.
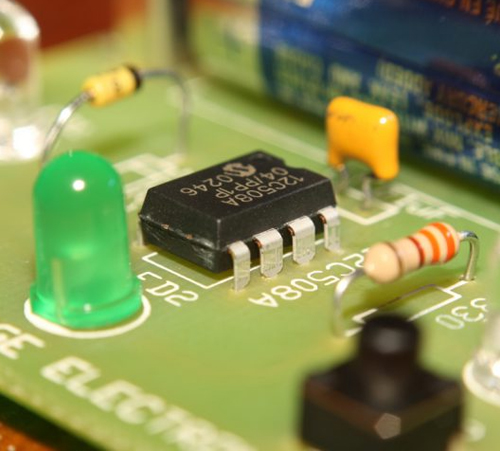
Advances in Ultrasonic Technology for the Electronics Industry
If you regularly clean electronic parts, an ultrasonic electronics cleaner is the best tool for the job. The common concern is that ultrasonic cleaners will destroy delicate components. However, advances in ultrasonic technology have eased this concern by replacing the single frequency wavelength approach—known to harm electronic parts—with a variable frequency approach, called “sweeping.” This advance in ultrasonic technology has not only led to reduced production costs, but has proven to enhance reliability, thus reducing warranty costs as well.
For PCB cleaning or when cleaning populated PCBs, the aim is to remove flux residues from PCBs, hybrids and DCBs. State-of-the-art PCB Cleaning processes are able to effectively remove all types of flux residues, ranging from RMA to newly developed synthetic materials.
Although the so-called „NoClean“ production has proved itself for many production purposes in the Low-End area, the cleaning of High-End assemblies is essential.
To ensure the reliability of bonding and coating processes, it is of utmost importance to clean the assemblies before bonding/coating. Resin and activator residues that lead to poor coating and bonding adhesion, as well as corrosion and electrical failure are not removed from the assembly during No-Clean manufacturing processes. Furthermore, lead-free solder pastes and flux systems newly introduced to the market during the conversion to lead-free soldering contain a higher content of resin and more aggressive activators.
Modern cleaning technologies have therefore been designed to cope with no-clean formulations, and with adequate equipment optimization this problem can be prevented. We offer water-based, semi-aqueous and water-free cleaning processes. Various cleaning systems are available for cleaning both lead-free and lead-based assemblies.
From left to right: Flux untouched, flux affected and partially removed, flux mainly removed, flux fully removed.