We feel immensely pleased to offer an exclusive gamut of Industrial Automation Systems. Our offered systems are manufactured by utilizing optimum quality raw materials and advanced technology by our skilled professionals. These include the combination of pre-cleaning, ultrasonic cleaning, rinsing, top air wiper, and hot air blow drying. In order to ensure quality, the entire range is rigorously tested on various parameters.
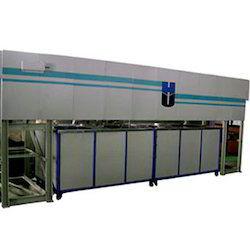
An industrial automation system refers to the integration of various technologies and control systems to automate industrial processes and tasks. It involves the use of hardware and software components to monitor, control, and optimize industrial operations, leading to increased efficiency, productivity, and safety. Here are some key aspects and components of an industrial automation system:
Control Systems: Industrial automation systems rely on control systems to regulate and monitor industrial processes. This can include programmable logic controllers (PLCs), distributed control systems (DCS), supervisory control and data acquisition (SCADA) systems, and other specialized control devices. These systems receive input signals, make decisions based on predefined logic or algorithms, and send output signals to control industrial equipment and processes.
Sensors and Instrumentation: Sensors play a crucial role in an industrial automation system by providing real-time data on various process parameters such as temperature, pressure, flow rate, level, and more. Instrumentation devices, such as transmitters and actuators, are used to interface with sensors and control equipment based on the received data.
Human-Machine Interface (HMI): An HMI is the user interface that allows operators or technicians to interact with the industrial automation system. It typically consists of a graphical interface displayed on a computer monitor or a dedicated touch screen panel. The HMI provides visual representation of process data, allows operators to monitor system status, view alarms, and perform control actions.
Communication Networks: Industrial automation systems require robust communication networks to facilitate data exchange between various components and devices. This can include Ethernet, fieldbus protocols (such as Profibus, Modbus, or DeviceNet), wireless communication technologies, and other industrial network standards. These networks enable seamless integration and coordination of different parts of the automation system.
Programmable Logic Controllers (PLCs): PLCs are widely used in industrial automation systems to control and monitor equipment and processes. They are programmable electronic devices that can execute logic-based instructions, collect input data, make decisions, and generate output signals to control actuators and other devices. PLCs are highly flexible and can be programmed or reprogrammed to adapt to changing process requirements.
Data Acquisition and Analysis: Industrial automation systems often include data acquisition and analysis capabilities to collect, store, and analyze process data. This can involve historian databases, data logging, trend analysis, and statistical process control (SPC) techniques. The analysis of data can provide insights into process performance, identify anomalies, and support decision-making for process optimization and predictive maintenance.
Safety Systems: Industrial automation systems incorporate safety systems to protect personnel, equipment, and the environment. These can include emergency shutdown systems, safety interlocks, alarms, and safety-rated devices. Safety systems ensure compliance with industry regulations and standards, mitigating risks and preventing accidents.
Integration with Enterprise Systems: Industrial automation systems can be integrated with enterprise-level systems, such as manufacturing execution systems (MES) or enterprise resource planning (ERP) systems, to enable seamless data flow between the shop floor and business operations. This integration allows for better planning, resource allocation, and decision-making across the organization.
Industrial automation systems have revolutionized industrial processes by increasing efficiency, improving quality control, reducing downtime, and enhancing worker safety. They are widely implemented across various industries, including manufacturing, energy, oil and gas, pharmaceuticals, and more. The design and implementation of an industrial automation system depend on the specific requirements and processes of the industry or application, and often involve collaboration between engineers, system integrators, and automation experts.